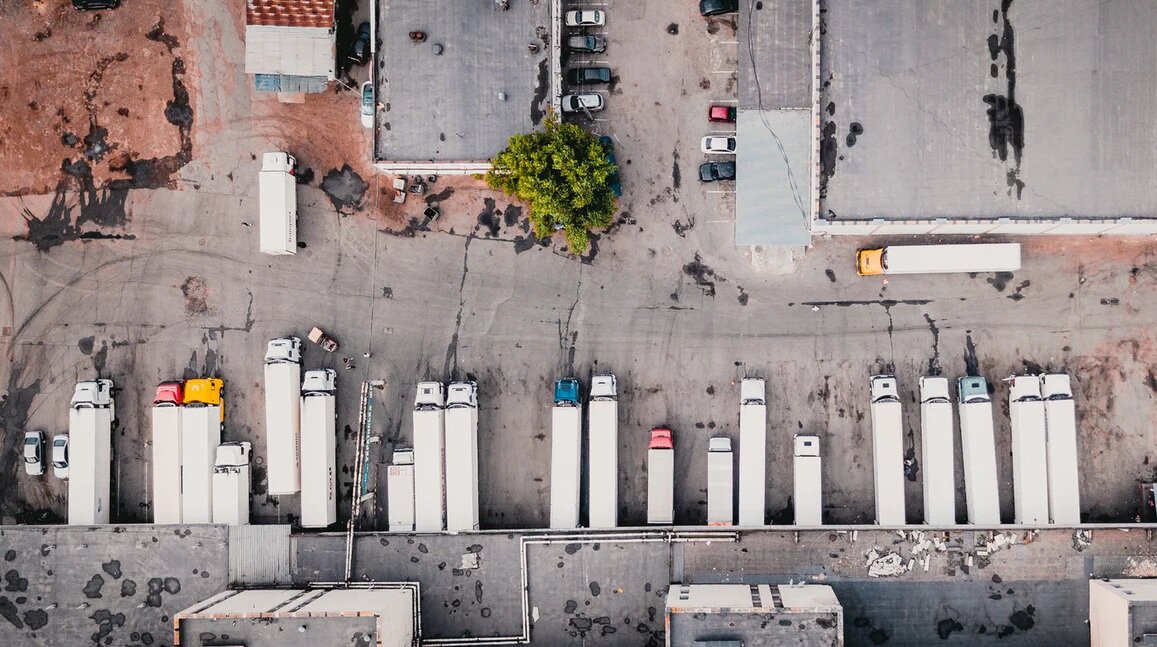
The Corso Systems Manufacturing Execution Systems Guide
Welcome to the Corso Systems MES Guide! If you are new to the concept of manufacturing execution systems (MES), the term simply describes the system which translates your business’ manufacturing needs into your production operations.
The Three Core Concepts of MES:
(Please note that an MES can grow well beyond these core concepts to fit the needs of any size manufacturing business or enterprise.)
Work Orders or Manufacturing Orders
Production Scheduling
Downtime Tracking/OEE
A MES System better equips your operations staff with information for manufacturing the right products at the right time. MES also gets information flowing from the plant floor back to the business folks so that you can improve the overall efficiency of your company as a whole.
We will dive deeper into these concepts throughout this guide and in our large collection of blog and tutorial content.
If you want to learn more about other aspects of manufacturing automation, please check out our PLC Guide, SCADA Guide, HMI Guide, and Industrial Information Systems Guide.
Need Help With Your MES?
Book a 15-minute call with Cody Johnson in Sales
No sales pitch, just a candid conversation.
MES Overview
A Manufacturing Execution System (MES) is the operating system for your business.
The MES integrates your company’s business systems with your production infrastructure—giving you the information to optimize operations from the shop floor to the top floor.
Typically with an MES, customer orders from the Enterprise Resource Planning (ERP) system are brought to the schedulers along with current inventory. The schedulers use this information to optimize the production schedule. You can even schedule days ahead so that your plant has time to prepare materials.
Next, the production schedule pulls in raw material quantities and alerts procurement when stock is running low. Your warehouse crews will receive pick lists and delivery times to ensure the plant has necessary materials. On the plant floor, the operators will run production with a SCADA system. Any slowdowns or stoppages are fed back to the scheduler to adjust future production runs.
We already have SCADA, why do we need MES?
As each production run is completed, the MES system alerts the shipping and receiving departments that product is coming their way—along with all of the paperwork needed to get things into the warehouse or shipped out the door.
MES is a force multiplier for your company. It can improve your business outcomes by giving your teams the information they need, when they need it. This will help them make the right decisions in real time.
Overall Equipment Effectiveness (OEE)
OEE is a single number calculated from a combination of factors monitoring the health of your process. Using OEE, you can prioritize maintenance, training, and material management activities to get the most out of your process—all without having to add new equipment or labor.
OEE is calculated as Downtime * Production Speed * Good Parts Produced (OEE = A x P x Q), and can be tracked over time to help you monitor system functioning both in short term snapshots and long-term trends. We will dive deeper into each of these trends below.
Example OEE Dashboard displaying OEE performance over multiple time frames
Need to Implement OEE?
Book a 15-minute call with Cody, the Corso Systems Head of Sales
Let’s explore the options together!
Downtime
Ideally, your equipment would run 24/7/365 and never stop producing parts. In reality you will experience a variety of minor shutdowns, maintenance issues, and process upsets preventing production.
Tracking these events is critical to your operation. Knowing the frequency and duration of your downtime events will help you prioritize fixing issues, and give you better insight into your facility’s weaknesses.
The first step in tracking downtime is understanding why your equipment goes down. Equipment downtime may be caused by mechanical or electrical issues, operator error, or machines downstream blocking or starving other machines of material.
Most systems include common downtime reason codes (E-Stop, Blocked, Starved, Maintenance, Other) and grow from there as the data needs to become more granular. These scenarios can be easily added to any PLC program to sort your downtime into actionable buckets. As the knowledge of your process grows, you can expand scenarios to encompass your specific needs.
Next, downtime events are processed into reports and dashboards to show you the most hurtful events, either by time, duration, or revenue impact. Now, you have the tools to fix the worst offending problems first.
Corso Systems example custom OEE Dashboard with downtime tracking features
To learn more about Downtime Tracking check out our MES 101 post on Downtime.
Production Speed
Production Speed is the measure of how quickly you can produce material. If your process is designed to make 1,000 units per hour and you are producing 800, you would be operating at 80 percent.
For most companies, this metric improves as they work to reduce downtime. Fewer minor stoppages mean that the average production rate will be higher.
Once you have optimized your Downtime, Production Speed will begin to have a greater impact on OEE. While it can be difficult to improve Production Speed—as we are all bound by the laws of physics—there are many process improvements you can make to improve your speed.
An enterprise doesn’t usually start their MES journey with Production Speed, however it soon becomes important to understand the controls you have over optimizing your operation.
A custom OEE Dashboard from Corso Systems showing Production Speed and the many factors impacting it, along with performance goals.
Read our Performance Management article to learn how to optimize your cycle time tracking.
Quality
Quality is defined as the number of good parts produced vs. the total number of parts produced.
Measuring quality is relatively simple. Is it a good part, yes or no? But, quality gets complicated when we begin to implement systems to answer this question.
Fortunately, we have tools like Laboratory Information Management System (LIMS) and Statistical Process Control (SPC) systems to help. These systems define the product samples you take and determine how the samples will be analyzed and stored. These samples feed back into the MES to provide a quality metric for your OEE calculations. We’ll dig deeper into the LIMS and SPC systems later in this article.
Custom dashboard displaying product quality analytics and piece/part data via Statistical Process Control (SPC)
We go deeper into the basics of quality management in our post on LIMS.
Scheduling
Production scheduling is a common first step into the world of MES. Scheduling can be implemented by itself, or can complement the implementation of an OEE project—adding visibility into specific production orders, shifts, and personnel.
Production scheduling starts with pulling in the required orders from the ERP system. Next, the system compares the orders with inventory on hand to pull from stock when possible. From there, the true power of MES begins to unfold.
Scheduling systems can determine an optimal starting point and automatically generate a schedule based on configurable rules. Once you have the planned orders for the day, the scheduler can make adjustments for any last minute changes and material shortages, then automatically generate all of the production orders.
The scheduling system handles the start and end times for batches while including changeover times. The plant control system continually feeds the real-time production data back into the schedule, alerting the scheduler of any potential impacts to future orders.
Scheduling allows you to lay down a solid foundation for building a more productive operation.
Want to dig deeper into scheduling? MES and machine scheduling post.
Statistical Process Control (SPC)
SPC combines process data with quality control data to give you powerful analytical tools.
The first step in implementing SPC is defining quality control samples. Typically, the definitions would come from an existing LIMS system, or any regular samples you are already collecting. Common samples are package weight or product purity, but they can be as specific and detailed as your process requires.
Next, the sample data goes into a database and analytical tools alongside your process data. The system provides control limits and quality trend scenarios. The control limits can be defined as basic min/max ranges, or complex algorithmic analysis tracking the number of increasing or decreasing samples.
If the samples are collected real-time, you can automatically adjust the process control tuning to improve quality during production. You can also analyze the data after production, and make adjustments for future runs.
SPC impacts the bottom line by reducing waste, scrap, and re-work. It helps you understand the causes of quality issues, and how to fix them.
Overall, SPC gives you a deeper understanding of how your process conditions affect quality.
Want to learn more about SPC? Check out the basics in our Acronyms Are Hard Series, or get more in depth with downtime tracking with our MES 101 Quality Management post.
Track and Trace
A Track and Trace system tracks raw materials through the production process and produces a comprehensive trace graph of each production step. For industries with regulated data collection—Food and Beverage, some Manufacturing, Aerospace—this is both necessary and valuable. But, Track and Trace can help any facility better track their production.
Track and Trace relies on your ERP and warehousing systems to pull in raw material lot numbers as they are used. This provides complete visibility into each and every lot going into each production step. As these materials are combined, your internal lot numbers are generated and stored at each step.
The Trace graph displays this information in an easy to follow format, showing you a complete picture of your products. It is then very easy to pull up production orders in case of product recalls, or simply understand which lot numbers contain which raw materials if you need to track down a quality issue.
Track and Trace is a powerful tool in the MES Toolbox.
We explore more details and options for Track and Trace in our post detailing the first step in a fully integrated supply chain.
Recipe Management
In conjunction with better production scheduling, a common next step is a recipe management system.
With recipes, you can define a set of setpoints for a particular product, ensuring the same conditions are used every time. If you are running new products, you can set up recipes which require approval before they can be run on the line, preventing unauthorized production.
Recipes are easily integrated into a batching strategy, allowing you to run multi-step production operations. And, all of these runs can be tracked using the other MES tools, giving you a complete picture of your plant.
Recipes can be as simple or as complex as necessary. When there are recipes for your products, it simplifies the information operators need to enter for starting production runs. Some facilities that have implemented recipes have been able to run a few additional batches daily due to the time savings from less typing alone.
Recipes are a powerful component of MES, and can unlock a lot of potential with your people and your process.
An example recipe management dashboard
Learn more about recipe management in our Sepasoft Solved Recipe Management video.
On Deck Production Orders
For processes running multiple products a day, we’ve found that using on deck production orders can help reduce changeover times.
As in baseball, an on deck production order is simply having the next order in line after the one currently running. On deck production orders allow an operator to get set up for the next order while a current order is wrapping up, then the next order can start automatically if there aren’t any changeover requirements. If there is a changeover, an on deck production order will simplify the process of selecting the batch and starting it manually.
On deck production orders give operations a view into what is currently running, and what is coming down the line, so they can be ahead of the curve for staging materials, labor, and equipment.
On deck production orders are one of the powerful tricks we have found along the way.
Ready to get On Deck Production orders at your facility?
Book a 15-minute call with Cody, the Corso Systems Head of Sales
No sales pitch, just a candid conversation.
MES Integrations And Tie-Ins
In this section, we’ll describe a few of the most common integrations that help our customers beginning their MES journey.
Enterprise Resource Planning (ERP) Software
One of the major integrations companies use is Enterprise Resource Planning (ERP) software. ERP is the backbone of the business. It includes customer information, inventory, purchase orders, accounting, scheduling and more.
Corso Systems has successfully integrated many off-the-shelf ERPs including SAP, JD Edwards, Oracle, Microsoft Dynamics, and SAGE. We’ve also worked with homegrown systems—so don’t feel left out if we didn’t list your ERP. If you don’t have an ERP, we can help you make the best choice for your company.
While there are many ways we can integrate your ERP, we’ll work with your IT department to find the best solution. Typically, we use a combination of web services calls and database access. Our partners also have supported solutions which easily integrate with standard ERP interfaces.
Why Would You Want To Integrate Your ERP?
An ERP integration allows you to use the information in your ERP without duplicating everything on the production side of the business. Most facilities that integrate with an ERP start with scheduling and inventory. This makes scheduling easier and more efficient. Since some facilities operate with a flexible number of operators, we can help schedule operators for your optimal performance.
Normally, we set up automated production data pulls from the ERP—plus we can integrate pushing data back into your ERP. A fully integrated system will allow you to streamline data entry and provide full visualization of your process. Imagine sitting down and instantly seeing your entire process from customer order to fulfillment. That’s what an ERP integration can provide.
Want to know more about ERPs? Check out Acronyms Are Hard: ERP edition. With an ERP integration, we can also help automate your company’s time cards!
LIMS
Does your company have a QC lab? Then you might have a LIMS, or Laboratory Information Management System.
LIMS features include workflow and data tracking, as well as the ability to exchange information across interfaces. Additionally, LIMS are important for facilities which need assurance that their information is up to date and accurate for regulators. LIMS data can be combined with process data using SPC to both meet your regulatory requirements and improve your production yields.
There are many off the shelf LIMS systems, as well as homegrown or custom built options. We have worked with just about everything under the sun including building our own custom systems. If you don’t have a LIMS and would benefit from one, we can help you make a selection.
Why Would You Want To Integrate Your LIMS?
An integrated LIMS will capture the most value from the quality data you’re already collecting. Integrating quality data with process control data is the basis of SPC. And SPC is one of the best ways to analyze and understand how your process conditions affect quality.
Correlating your lab testing data along with your manufacturing environment is invaluable. Now, if there is an issue, you can quickly and easily see all the information about the pieces involved. You can also track materials back to their source and find any other pieces that need to be checked.
The visualization of your process will be much more complete once you have integrated laboratory testing. Learn more in our post, Acronyms Are Hard: LIMS edition!
Plus read about a custom LIMS solution Corso Systems created for an Oil and Gas facility.
Cameras
Everything seems to have a camera these days. Likewise, many facilities are starting to use IP cameras to watch their process in action. Operators can view an entire machine from the control room. And confined or otherwise dangerous locations can be constantly monitored.
Many platforms we use for MES integrations also support camera displays—some even record and store video. Combined with modern cameras utilizing MQTT motion alerts, you can get a complete picture of your process as soon as any anomaly occurs.
We also work with many companies who use temperature monitoring cameras, such as FLIR and Fluke. These can easily generate images for reports, or can be integrated with your SPC and/or LIMS systems to correlate images with quality and process data. These cameras can also notify you if something is trending out of spec.
Beyond simply capturing images, we can also run predictive analytics on the camera feeds to preemptively predict failures or abnormal events.
Vision systems provide insight into your process beyond operator capability. They can optimize part layout on a pallet, increase cycle times by adjusting spacing on the line, or test parts for quality control at a rapid speed.
Why Integrate Your Cameras?
Integrating your cameras is a great way to view your entire process. Many facilities already have cameras installed which we can integrate. Even relatively inexpensive cameras can produce better process visualization.
Adding cameras for temperature monitoring or other advanced vision systems can exponentially increase overall productivity.
Learn more in our article, Intelligent Automation Pyramid: Business Intelligence Systems.
System & Machine Login
Many facilities have ID badges for their staff. Along with inexpensive hardware, operators can login with a badge swipe. Additionally, biometrics such as fingerprints, retina scans, or even NFC sensors in a phone can be used to login.
Integrating automated logins with your MES and SCADA systems is an important step for several reasons. It eliminates extra typing and removes the need to operators to remember passwords. Operators can login more easily to the system, and you will know who is running a system or machine at any given time.
Integrated automated logins simplify machine and settings access management. You can easily lock down recipes and setpoints, then require specific user rights to make adjustments. You can also link training records to your employees and prevent them from operating machines before they’re trained and qualified.
Finally, integrating automated logins removes a step in employee onboarding or role change. Their access can be linked to their training and badging process. They will no longer need to contact the controls team for access, they will already have the access they need when they are entered into the badging system.
Advantages of Integrating System & Machine Logins
Integrating logins reduces operator password issues. It simplifies managing access to everything, and helps put you on the path of always having machines running at their optimal settings.
Integrating automated logins with your MES allows for automating your time cards from any location in your facility.
Additionally, you can use these integrations for easier scheduling.
Barcode Printers & Scanners
Barcodes reduce data entry requirements and can be a powerful transformative process for many facilities. Imagine getting rid of clipboards and scrawling down—then trying to read—complex part numbers and recipe codes.
Instead you can create barcodes and use the MES system to generate printouts on stickers (or etched directly into parts). Then, the parts only need to be scanned into use.
Regular barcodes, QR codes, or any type of complex custom barcode can be integrated with a modern SCADA and MES system. You can even enter supplier product SKUs and scan in raw material information, lot numbers, and more using the same barcode system as your process.
Using barcodes can help eliminate mistakes and make everything move faster. It reduces operator fatigue and lets them focus on what they do best.
Advantages of Integrating Your Barcode Printers & Scanners
If you’re frustrated with pencil and paper and want to move into the digital world, then barcodes are for you. At Corso Systems, we have helped companies serialize every part before it goes out the door, integrating data into their customer facing systems for a complete lifecycle of every part they sell. Using barcodes makes this easy.
Embrace the transformative process, and find efficiencies you didn’t know existed. Learn more in our Track and Trace post.
If you’re not sure whether a particular integration exists or can exist, the answer is probably YES and you should definitely ask us about it immediately.
MES Software and Platforms
Still want more? Let’s talk MES System software.
There are many software platform options for building an MES system. We have extensive experience working with a number of different platforms, because that’s what we do. We’ll touch on our top three favorite software platforms below, and if you have questions about others, we’re be happy to discuss more details.
Inductive Automation’s Ignition
Inductive Automation’s Ignition has taken the industry by storm with their novel pricing strategy: one price. It’s a beautiful thought, and not needing to keep a running count of clients, tags, and PLCs makes it easy to figure out what software licenses you need. The list of Ignition customers is impressive and includes Tesla, Amazon, Coca Cola, Johnson & Johnson and many more.
At Corso Systems, we have leveraged Ignition to produce some magnificent results. Corso Systems is extremely proud to say that we are Premier Integrators and all of our controls engineers are Gold Certified in the latest versions of Ignition!
Read more about Corso Systems and Inductive Automation Ignition.
Siemens WinCC Open Architecture
Siemens’ newest iteration of software has Open Architecture flair. Happily, this allows for more customization and templating in the software than previous versions—and increased speed of implementation.
A big reason customers consider OA is how fast the process historian can collect data, and the huge amount of data the process historian can store. How huge? At CERN, they use OA with the Large Hadron Collider!
The overall look and feel of WinCC OA is very nice and many applications happily call OA their MES provider.
Corso Systems is proud to be a Premier WinCC OA Integrator. We also completed the very first US-Based oil and gas project on OA.
Read more about WinCC OA here.
Rockwell Automation’s FactoryTalk
Everyone likes to compare FactoryTalk to IBM in the 80’s and 90’s: no one ever gets fired for using FactoryTalk.
Historically, FactoryTalk has been a bit disjointed with integration of purchased modules, but interesting developments have come from them recently. Facilities which use Rockwell Automation for hardware often consider FactoryTalk, since they are usually comfortable with Rockwell. Others have used FactoryTalk in the past and want to continue to use it, which is a totally valid reason.
We have FactoryTalk experts on staff, and we get a few calls a year from production facilities that need us to save their integration or perform a migration with our cross platform knowledge.
Thanks for Reading our MES Guide
If you’ve made it all the way to the end, we really appreciate the amount of time you’ve spent with us!
Manufacturing Execution Systems serve as the backbone of your manufacturing operations, seamlessly integrating business systems with production infrastructure. From optimizing work orders and production scheduling to real-time tracking of downtime and overall equipment effectiveness (OEE), MES empowers your team with actionable insights for making informed decisions.
We hope you enjoyed this constantly updated MES Guide and maybe thought of a few ways that your facility could benefit from implementing a Manufacturing Execution System, or expanding on the system you already have. If so, please reach out and share your project—especially if you’d like to learn how Corso Systems can help you integrate any of your existing equipment or production systems. We’d love to help you do what you do better than ever.
Ready to optimize your manufacturing operations?
Book a 15-minute call with Cody, the Corso Systems Head of Sales
No sales pitch, just a candid conversation.