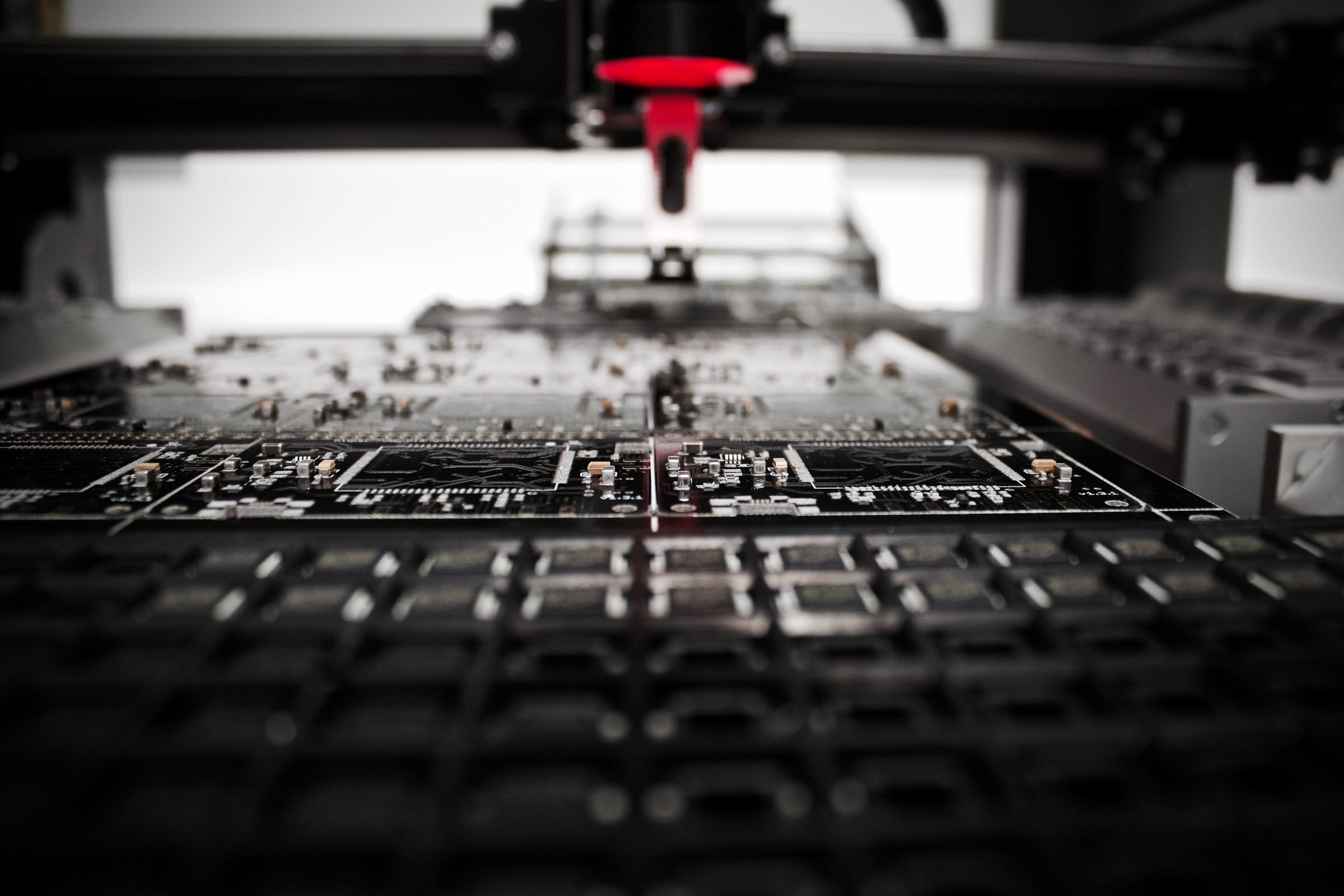
Programmable Logic Controllers (PLC)
Programmable Logic Controller (PLC) Programming Overview
PLCs take the operator’s commands from the SCADA system and turn them into reality.
They provide the signals to control equipment and the logic to ensure things happen safely—in the correct order.
Programmable Logic Controllers make your process as repeatable as possible.
PLC programming typically uses ladder logic, a language designed to mimic relay logic, the predecessor to PLCs.
Many modern PLCs can be programmed in multiple languages, defined by IEC 61131-3 standards. These languages include:
Structured text
Function blocks
Sequential flow charts
PLCs can now use object oriented code—so you can build reusable code to save development time and costs.
PLCs, robotics, and other automation tools perform the monotonous, strenuous, and dangerous work instead of your operators—so that operators can focus on tasks best accomplished by humans. Automation increases the productivity of your process, improves quality, and helps your people get more done in the same period of time.
When properly designed, PLC logic can also be a powerful troubleshooting tool for maintenance staff. Like any programming languages, it requires skill and experience to write efficient and error-free code. And, it only needs to be as complex as absolutely necessary. When something goes wrong with equipment, a PLC can be your most valuable tool to get the process up and running again quickly while reducing downtime.
Automation saves money, operates your equipment more safely
and increases your facility’s throughput.
The Corso Systems Philosophy of PLC Programming
After spending significant time deciphering other people's code in the past, we focus on writing structured, well-designed PLC code. This approach assures that we create a flexible, easy to understand system which can be modified for future needs. We’ve developed and tested libraries of code which are currently running some of the top facilities in the world. Much of this is also available for new systems and projects.
Put simply, our goal when programing PLCs is to build a system anyone can maintain in the future. Our customers should never feel like we are the only resource available to maintain their systems.
Our PLC Experience and Service Offerings
We can develop new PLC programs from the ground up, and can troubleshoot, update, and modify existing systems anywhere in the world. We are experienced with Siemens, Allen Bradley/Rockwell, Modicon/Schneider Electric, Omron, Automation Direct, SCADAPack, and others, including Safety PLCs.
Corso Systems can integrate PLCs with other devices and systems including—but not limited to—HMIs, manufacturing execution systems, databases, drives, and RFID and barcode scanners. We can also work with any industrial network protocol or hardware layer, including Profibus, Profinet, ControlNet, DeviceNet, Ethernet I/P, Modbus, RS-232, RS-485, HART, and others.
In addition to controlling process equipment, we also develop software libraries, APIs, Add-On Instructions (AOIs) and function blocks enabling end users to easily integrate your PLC platform with any other hardware or software.