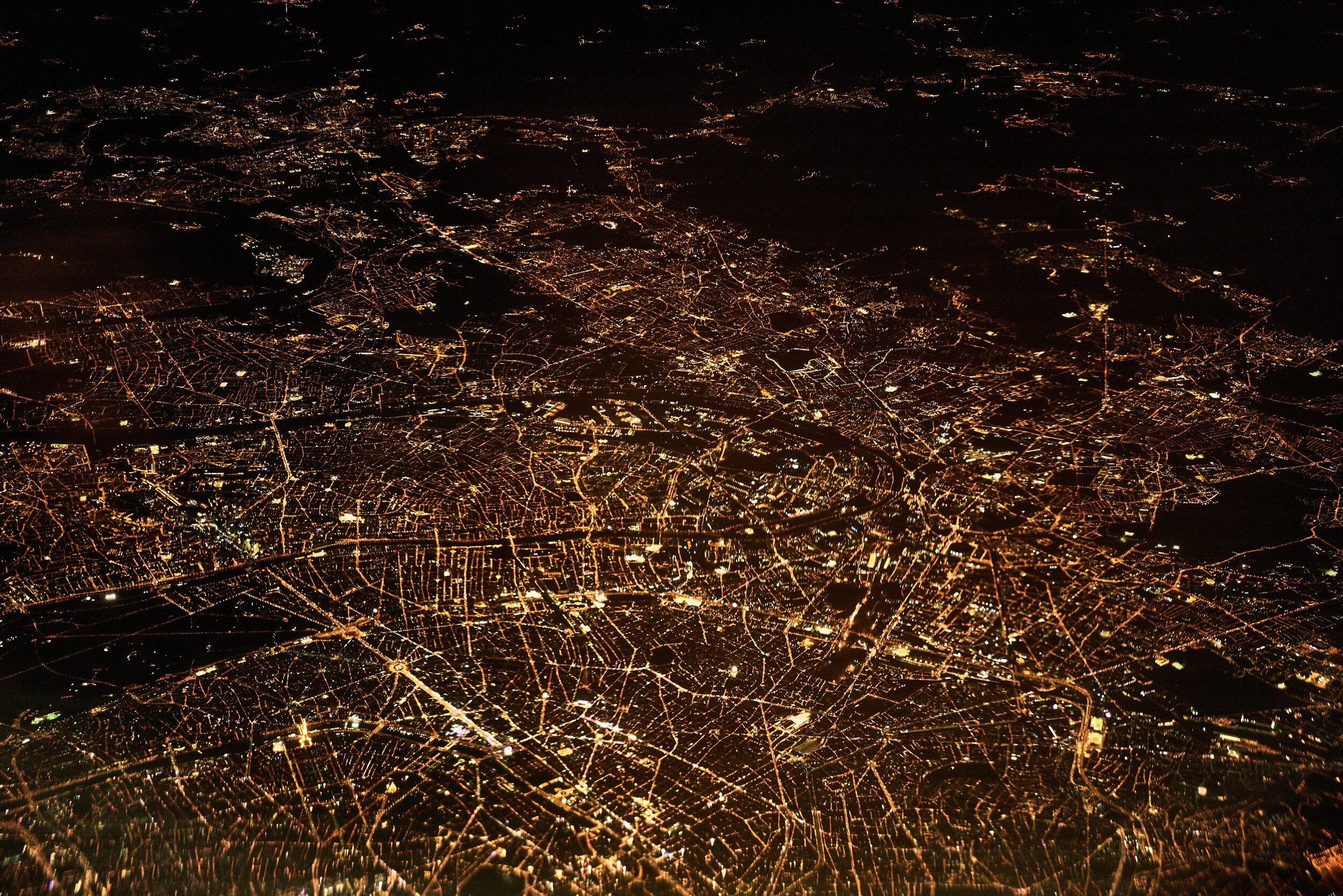
Industrial Information Systems
We live in a world of rapidly increasing technological innovation. The amount of data available is at an all-time high, and can be a valuable asset when it’s accessible and put to use. Production and manufacturing facilities are no stranger to this data, with statistics from machine-level performance to a full facility overview. But, the data itself only paints a small portion of the larger picture. Having the tools and knowledge to analyze this data brings a facility into the digital world, and Corso Systems has years of experience in this sector.
Industrial Information Systems (IIS) are one of the key solutions Corso Systems provides for utilizing this data. Our solutions increase production, efficiency, performance, and capacity at facilities—which in turn increases output and revenue. IIS solutions also serve as a glimpse into the future of a facility, showing where problems may arise ahead of time based on past trends or current limits and thresholds.
Many facets of Industrial Information Systems are integral parts of overall plant automation. They cross into the areas of MES, SCADA, and PLC implementations. If you’d like more info on these systems, head over to our MES, SCADA, and PLC pages for more information.
Corso Systems has developed many custom Industrial Information System Solutions. We also integrate other software platforms depending on the needs of a specific plant. Some of the systems and solutions we use and develop are outlined and discussed below.
Business, Administrative, And Web-Based Solutions
Not all of our work is solely focused on the plant floor. As part of a “top floor to shop floor” integration, we normally interact with business-focused tools.
Business and administrative applications often include:
Project management tools
File system integrations
Training systems
Employee scheduling
Energy management
Accounting and financial software packages.
For your sales team:
An example of this type of business/administrative integration would be software like SalesForce. We can integrate the data your sales team inputs to better track customer information and orders. Salespeople can then see the production schedule and warehouse inventory levels to get a better idea of available timelines to slot in a customer order. They can also be alerted when production orders are completed and ready to ship, or delayed for any reason. The sales team can be proactive in managing their relationships with real-time data, making for happier customers overall.
For customers:
If you want to have a more transparent relationship with your customers, you can even give them access to a sanitized version of the information. Then they can see generic schedule blocks for orders for other customers, reports and quality test results for the lot numbers they are purchasing, and dashboards for their orders as they are run on the line.
For your production crew:
Another common integration involves user roles in your system based on training. If a particular user hasn’t been trained on a piece of equipment, this can be tracked. Automatic reports and alerts can ensure employees receive the training they need in a timely manner. And they can be prevented from operating machinery until they are trained.
For your maintenance crew:
The same concept can be applied to maintenance, giving your maintenance teams real-time information on the state every machines. They can then keep the plant running smoothly by prioritizing their workload.
Developing Your Systems:
Many of these systems are off-the-shelf, or internally developed tools. If there is a way to get data into and out of a system, we can integrate it into your overall IIS strategy.
Contact us to start a discussion on your business information system needs.
Databases And ERP Systems
Databases
Databases are often the back-end portion of Industrial Information Systems. Databases store large sets of a company’s data: production order details, production data, or employee information.
Databases are the primary tool used to store data for information systems. Many of the solutions Corso Systems provides integrate with client databases to track different portions of a manufacturing process. From raw material information in a warehousing system, through the production process as this material is consumed and turned into finished goods, and through the shipping process. All of this is accessible in our tools. Corso Systems constructs interfaces to interact with this information to create automated selections based on the required end product. This allows users to select items in a user-friendly interface, see what raw materials are available, and have visual feedback on each step of the operation. This simplifies the process for accessing data, managing what’s manufactured in a facility, and allows any authorized user to access and follow the information clearly.
Many companies have a database management system already in place, which we then integrate with other systems, and add to or amend as needed. Some companies do not have a well-managed database management system yet, but may be using tools like Microsoft Excel to store and track different products or parts in their facility. Corso Systems has helped these companies create a robust information management system that is easily operated through a company-specific user interface to help this important data be used to its full potential.
We have worked with companies in all steps of the database management system process, and created solutions customized to fit each need.
Major database management systems we work with on a continued basis include (but are not limited to):
Microsoft SQL Server
MySQL
Oracle
PostgreSQL
IBM
SAP
Enterprise Resource Planning (ERP) Systems:
ERP systems are used by companies to store their business and operational information. ERP systems are usually a higher-level, more structured software that with a database backend. They tie all of the operations of the business together, giving a complete business picture across all departments. Everything from customer orders and purchasing receipts to human resource and distribution information can be tracked in an ERP system.
With different tie-ins and modules supporting different functions for different business levels, ERP systems can be used different ways by different departments. At Corso Systems, we often tie ERP systems into our MES solutions to get the most benefit and visibility out of the stored information. We can do this at every level of a company, from administration to production.
Integrating your ERP system with an MES solution creates many benefits for running efficient facilities and allows you to see what is happening at every level of your business. You’ll be able to push and pull data to and from your ERP system automatically, schedule runs and recipes to run at specific times in any part of your plant, manage recipes and inventory, and track products from start to finish in a manufacturing process. You will be able to see what is arriving at your facility, when, and how much of it you have. You can use this information—along with customer order info—to schedule different product runs based on what you have and what is needed to fulfill orders. Everyone in your facility will be working on the same page with total plant visibility. They can streamline their workflows, all while using a custom-designed user interface to understand the data and easily follow the process.
As with database management systems, we have worked with companies at all levels of ERP development and integration, and are happy to assist with design and recommendations. Some of the major ERP systems we work with on a continued basis include:
SAP
JD Edwards
Oracle
Microsoft Dynamics
SAGE
Epicor
Contact us to start a discussion on your DBMS/ERP needs and our Industrial Information System solutions today.
Manufacturing Execution Systems (MES)
Manufacturing Execution Systems contain many individual Industrial Information System solutions as part of a total MES package. Shoot over to our MES Page for a more in-depth explanation of these solutions, and we will touch on a few key analytical pieces here that help bring important plant information to the forefront of your process.
Overall Equipment Effectiveness (OEE):
OEE, or Overall Equipment Effectiveness, allows facilities to track three key areas of production. OEE uses a pre-calculated, site-specific formula to follow Availability, Performance, and Quality factors. These factors all play into your overall OEE percentage, which is valuable metric to see how a manufacturing process is actually operating. OEE systems allow you to peer into each of the three individual metrics, as well as see how they are working together as a whole.
Availability shows equipment, line, or facility uptime vs. downtime (depending on the granularity of your system). This can be used to track planned and unplanned production shutdowns, equipment errors, continued problem areas, etc. as well as see the exact cause of those errors on an easy-to-use user interface that is completely automated
Performance is related to downtime in a sense that less downtime is a good way to increase production. The longer your equipment is running, the more parts you can create. We use information and feedback from many different pieces of equipment to show just exactly how much product is being created at any single time, and what those numbers look like by hour, shift, and or day to build a bigger picture of a process in visual form.
Quality is similar in that the more good pieces you produce, the less waste you have. Finished goods that must be thrown away or re-worked due to subpar quality cost time and money in lost materials. Using processes to rework previously manufactured items that weren’t up to standard instead of producing a quality product the first time also lowers production and availability factors, further lowering your plant’s OEE.
For more detailed information, check out our page on OEE and Downtime Tracking
Statistical Process Control (SPC) and Laboratory Information Management Systems(LIMS) Integrations
SPC and LIMS are best utilized when tied into a larger overall MES system. These systems use testing and analytics from a facility’s lab environment and/or research and development department to set predefined standards and metrics for whatever is being manufactured. They also track live runs and do real-time comparisons. Using this standard set of data to compare against live production values can warn plant operators and managers of many issues that could arise during a run. Parts run outside (or close to outside) of a predefined spec range, trending of current and past runs, and quality improvements can all be seen and made using these systems with the help of advanced analytics. We create user interfaces for these systems to help you understand what is happening on the production floor, as well as make real-time adjustments to your system if it is necessary. These analytics are saved and can be compared to adjust for future runs..
For more details, check out our pages on SPC and LIMS
MES systems include a large variety of other analytic tools and tie ins for Industrial Information Systems. These include solutions such as Production Scheduling, Track and Trace, camera integrations, and barcode printer and scanner integrations. Head over to our MES page to see more.
Contact us to start a discussion on your MES needs and our Industrial Information System solutions today.
Process Historians
Process Historians are vital for a manufacturing or process-related company. Whether process historian software is used for audits, historical production information, or proof records for industry standards, these systems serve as an important addition to manufacturing facilities.
Process historians store large amounts of facility data in a safe, easily retrievable, and organized fashion. This information is often used for various reasons, so easy navigation and a user-friendly interface are important pieces when choosing a process historian.
Historians store process tag data on a server for easy recall at later times. This data can be used to compare previous production runs and analyze what was happening in a facility at any given time. Depending on the granularity of your process, this data can be set up to be stored in many different ways. Historians can automatically record tag data using high-speed polling. And they can store information for process values, production information, systems performance information, and much more. Historians can pull this data from many different types of equipment as well—from a PLC running your HVAC system or a motor running a mixer in one of your storage tanks. This data is displayed in a visual user interface that is navigable and understandable when properly developed, making it a powerful data analyzation tool.
Corso Systems has experience working with many different process historian providers. Here are just a few of the providers and solutions that we have worked with:
Canary Labs Data Historian
FactoryTalk SE Historian
OSIsoft PI Historian
Siemens SIMATIC WinCC OA
Wonderware Historian
Process Historian Migrations
Some companies have found that their historian needs have changed as technology continues to progress. This can be due to functionality found in another historian, issues with support costs, results being out of alignment, or simply wanting to move to a different historian provider.
We have worked with many companies to migrate to a new historian platform, along with data migration to ensure they have all of the data they have collected over the years available in the new system.
Our easy-to-use automated tools collect all of the configuration data from an existing historian, export the data, and then migrate everything over to the new historian. This can be done without any downtime. Our tools include analytics and diagnostics allowing you to see what was imported, if there were any discrepancies, and allows you to decide if any data needs to be cleaned or purged before importing into the new system.
These tools work with historians of any size, and can convert just about any historian to your new platform. Our tools even support moving SCADA system based historical data from software such as Ignition, Wonderware, and FactoryTalk View into a proper database backed historian.
Contact us to start a discussion on your Process Historian needs and our Industrial Information System solutions today.
Reporting: Trends, Graphs, Charts, Alarm Notifications
Reporting is a powerful tool in the world of information systems. Reports are often visual, consisting of charts, graphs, and trends, which allow users to see the data in a different form. Aside from showing numbers in a visual form, this information gives you valuable data points to track and compare.
Trends
Production trends can be used in real-time or in a historical form. Watching a process live can show what is happening and where, but may not provide a complete picture of an entire production run. Historical trends for processes can be a great analytical tool. They give information on what happened—and exactly when it occurred. These trends can be configured to record any data point in a process that is brought into the historian. This allows you to see what is happening at exactly what time with any piece of equipment or instrument you are tracking. This trending can be expanded to see individual production lines or whole production departments and compare data across your entire operation. Comparison of these trends allows you to pinpoint any issues or points of constriction in a process, and devise plans to streamline these points to help increase efficiency in the manufacturing facility.
Graphs and Charts
Graphs and charts can be used in a similar form as trends. They’re also better for displaying aggregate information for days, weeks, months etc. This information can also give you an idea of where the strengths and weaknesses in a process are—and why the production numbers look like they do. Information from an MES system can be sent to these types of reports, which can include different information such as downtime and reasons, quality, and overall production numbers. These data points are integrated into graphs and charts to visually explain what your process is doing and why.
Alarm Notifications
Alarm Notifications can be used to warn you of impending issues before they happen in a process. You can set alarms on any data point to warn of values that do not match what’s required in a manufacturing process. This means you can be warned of a value that is trending out of an accepted range before it reaches that value by using upper and lower threshold data. This gives you and your operators time to react and correct the system before it is too late, ideally saving a product before it has to be reworked or scrapped. Contact us to start a discussion about your Reporting needs and our Industrial Information System solutions today.
Industrial Information System (IIS) Products
Many of the software providers we use for integrations have built-in Industrial Information System tools. We are comfortable using any platform, even if it isn’t listed, and we have even created many of our own custom solutions to solve unique challenges that we have faced over the years.
Inductive Automation Ignition
Inductive Automation’s Ignition provides many different modules that cover different industrial information system solutions. We have worked with many of these modules, including third-party modules and modules developed by Inductive Automation. Corso Systems also develops custom modules to solve unique problems our customers have that can be solved using the Ignition platform. The available modules range from alarm notifications to reporting and barcode scanner modules. Some of the information system module development companies we have used with Ignition projects include:
Inductive Automation
Sepasoft
Cirrus Link Solutions
Kymera
Learn about how we’ve worked with Inductive Automation’s Ignition as Premier Integrators to deliver ISS solutions, or contact us to start a discussion on your needs and our solutions today..
Rockwell Automation’s FactoryTalk
Rockwell Automation has provided industrial control software for many years. They have quite a few solutions for Industrial Information Systems as part of their FactoryTalk suite of products, including analytics, historians, backups, and many more.
Head over to our Partners page to discover more product options.
Siemens WinCC OA
Siemens is another name familiar to those in controls and automation. They provide many of the similar products to those above in their WinCC OA platform. Head over to our Partners page to discover more product options.