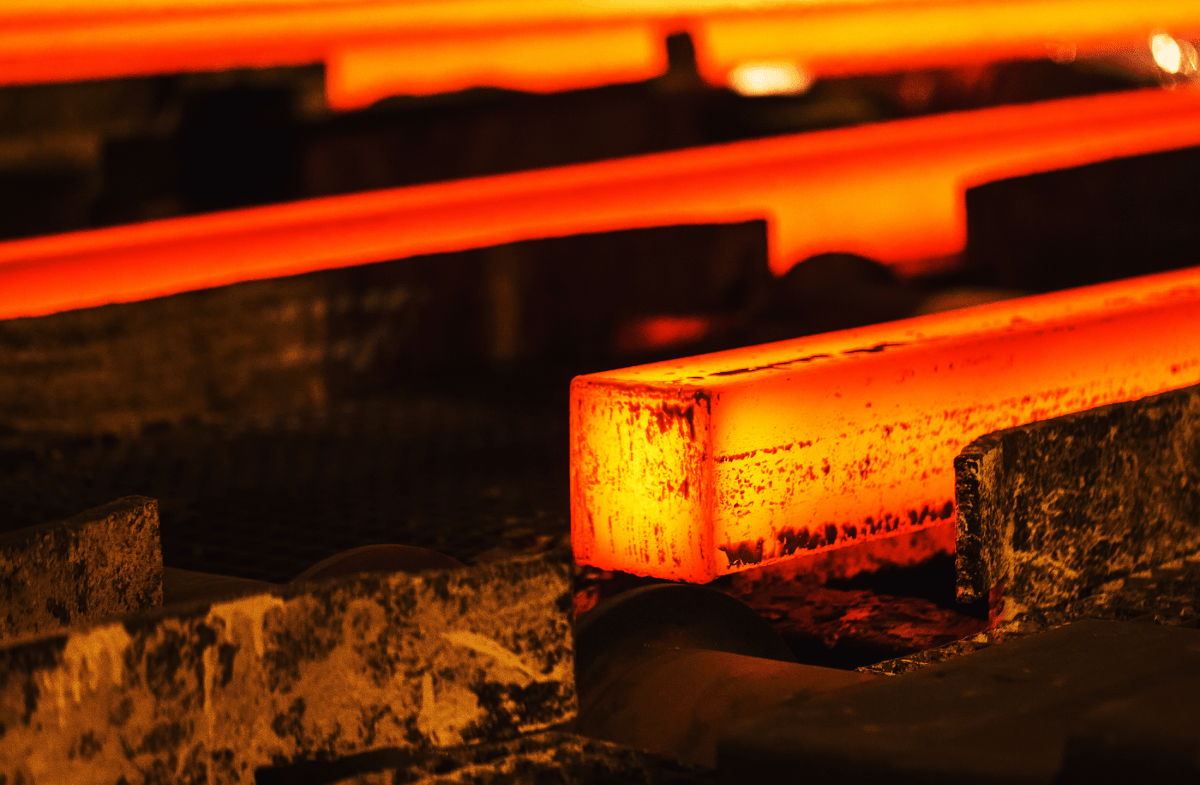
Heat Treat Power Pack
An operator at a heat treating facility in the rolling fields of Illinois closed the door on one of their furnaces to start a batch, walked over to a grungy whiteboard to write down an order number and the time it needed to come out of the furnace. The company had been in operation for over a century, and it seemed some of their procedures were almost as old as they were.
The parts being heat treated were anything but ancient. Aerospace materials made out of complex alloys, automotive parts, and turbine blades were some of the things you’d see coming out of the furnaces on any given day. In another part of the plant robotic arms tended to CNC machines for almost fully-automated machining operations, and a complex ERP system was in place to manage all of the orders they processed for customers all over the world.
As with most heat treating companies the furnaces were the cornerstone of their operation, and were always deemed too valuable to update. Over time they had become the bottleneck preventing the company’s growth. At some point in the previous decade there was enough downtime to retrofit the 6 flagship furnaces with PLCs and a very costly SCADA system. This was great for basic data collection on the furnaces, but was limited in what could be integrated and displayed outside of each furnace’s control panel. Due to the cost and hassle of adding a TV display to the heat treating area a white board was still used to track when batches needed to come out of the furnaces.
Management knew it was time for a change, and they worked with Corso Systems after a referral by a Chicago-based heat treating company to help. Everyone’s ears perked up when they heard we helped run 2 more batches through each furnace per shift simply by removing the need for manual data entry on each batch. The savings on the annual license cost of their existing SCADA system would pay for the entire upgrade, including the Ignition SCADA platform, within 12 months, and would provide a foundation they could use to integrate with the rest of the facility. This helped them streamline processes across the entire company, provide more detailed information to their customers, and dramatically increase product quality.
The dingy whiteboard that had ceased to be white over a decade ago was replaced with a TV. Every furnace was tied into the system, orders were able to be called up automatically based on the production schedule, purging and pre-heat operations completed with no operator intervention, and recipes were set to run once the furnace was loaded. In addition to running full loads of individual parts, the system could monitor what batches were on deck and correlate smaller runs into grouped batches with similar heat treat requirements to speed up production.
Every batch run through the furnaces was automatically updated in the ERP system providing a PDF report with all of the batch information including temperature graphs, gas usage, and overall energy costs per batch. This could then be integrated with the customer service portal giving customers real-time visibility on their orders.
Downstream processes were alerted when batches came out of the furnace and were ready for further processing with plant floor displays installed throughout the facility for everyone to see what was going on across the plant floor.
No one ever had to walk by that whiteboard ever again and check the clock to see if a batch was ready to come out. The operator in charge of unloading the furnaces got a text alert 10 minutes before the batch completed so they could get everything staged to turn the furnaces over as quickly as possible.
Corso Systems, Heat Treatment Process Experts
Corso Systems has helped many heat treat companies to standardize, optimize, and automate furnace operations. We have helped companies who manufacture and heat treat springs, tools, medical devices, and steel - from common everyday products to the most advanced aerospace and nuclear reactor parts.
Regardless of what you produce, we believe transparency, technology (including automation), and training are the best tools to take your manufacturing and heat treatment operations to the next level.
While some heat treat companies are now completely paperless with fully automated furnaces, conveyance systems, and integrated business systems, other facilities are still running in manual mode with no automation and very little technology. Predictably, many others are operating somewhere in the middle. But, no matter where you are on your journey, Corso Systems can help you get to the next level.
What is the Corso Systems Heat Treat Power Pack?
In our experience, manufacturers who have heat treatment in their process can get the most bang for their buck in five areas. Each of these areas focuses on maintaining and improving quality, customer satisfaction, and enhancing overall peace of mind for your company.
Because many heat treating companies can benefit from them, we call them our Heat Treat Power Pack:
If you’re already doing some of these, great! If you are doing all of them, that’s even better! But, if you need help implementing them for your heat treat operations, you have come to the right place. We can get you up and running quickly in any or all of these areas, giving you the tools to run your processes at their potential!
In this article, we’ll explain each aspect of the Heat Treat Power Pack below. It is built with hardware and software that any company familiar with automation can work on. You will also have full access to all of the code included with the deployment—and you own all of your data and information. We will take care of the hard work for you.
Ready to Power Up Your Heat Treatment Processes?
Book a 15-minute call to find out how we can help!
No sales pitch, just a candid conversation.
Continuous Data Logging
Whether you have a single furnace or twenty, continuous data logging will allow you to monitor your operation 24/7. If your furnaces are already controlled by a PLC or a control system like a Honeywell HC900, then we can help you set up remote monitoring right away. But, if not, we can also help you get the most from your existing equipment by adding automation to your setup.
Important furnace data points we can help you collect include:
Temperatures across your furnace(s), including overloads
Gas and energy usage
Process conditions such as atmospheric conditions, vacuum conditions, and humidity
Quench duration and rates
Ramp duration and rates
Soak times
Process alarms
Motor and bearing conditions
Current parts, recipes, and setpoints
Connecting your PLCs and/or Honeywell controllers with a SCADA system such as Ignition by Inductive Automation is a smart option for a low cost, highly functional automated system for collecting data from any equipment or process in your facility. Many heat treat companies are already enjoying the benefits of systems just like this installed and integrated by Corso Systems. These manufactures can make data driven decisions with ready access to many years of data, along with real time process data. This can allow you to monitor your equipment for overall product quality, anticipate maintenance needs, manage utility costs, and keep track of overall equipment health.
Work Orders, Recipes, and Variance Tracking
Many heat treat processes have travelers which move along with parts, specifying all of the relevant information—including which recipe needs to be selected on the furnace. Unfortunately they usually don’t include much (if any) validation to check if the operator has entered the correct data when running the part.
But now it’s easier than ever to build a system to collect the data normally shown on the traveler and pull it up automatically so that the operator no longer needs to manually key in the information to the system. Now, the system can easily include a recipe for any operation in your facility, populating the setpoints on your equipment—along with tracking when a batch was started, when it finished, and everything that happened in between. You can even use the batch running to trigger printing tags for quality control, and even shipping the part out the door.
While using recipes, you are also automatically set up to monitor for variance tracking. If your operator changes a setpoint mid-run, or it drifts away from normal values, you can track this information and alert your operators before anything goes out of spec.
In many cases, upgrading from a traveler system to a work order system allows operators to run an additional 3-4 batches per day through a furnace with the amount of typing saved. This also drastically reduces the impacts of mis-keying information, since it is automatically entered after the operator types in a work order number.
Production Dashboards, Trends, and Data Analysis
With furnaces running batches based on work orders and recipes (while collecting data on relevant aspects of your process), you will want to display what your equipment is doing. This is where production dashboards and trends come into play.
Production Dashboards provide a real-time view into your process. You can observe trends in temperatures, utility usage, quality control sample testing, and even the real-time status of your process instruments and field devices. These dashboards can be consolidated into a control room, or displayed across the plant floor to give your operators convenient access to the information they need to run your heat treating systems.
You can use trending tools to drill into your data in real-time or historically. By comparing the current run of parts against previous batches, you can evaluate how you are performing and quickly spot any anomalies. These trends can be saved to access again in the future, or exported to print out or send to your team via email.
Your new automation system can even export any data from any batch to Excel or other data analysis tools so you and your team can use any favorite or familiar tools to dig into the data.
If you aren’t collecting data yet, it will difficult to analyze your process, and trying to take data from an outdated chart recorder and import it into Excel is an exercise in frustration!
It’s time to move beyond paper and into the digital age to get the most out of your equipment, people, and processes.
Reports
If dashboards and trends are useful for operators while running the process, reports are useful as summaries of what happened during a run. Depending on your industry, you may also be required to generate and store reports about each production run.
With the Heat Treat Power Pack’s reporting functionality, you can easily generate daily, weekly, monthly, etc. reports. We can also generate reports during a run based on process conditions, various configurable triggers like timers, reaching a ramp/hold temperature, completion of holds and ramps, if various alarm conditions are hit, or anything else you might want to know.
These reports can be stored electronically as a PDF, emailed, printed, and summarized into a single file at the end of a run if you are generating multiple reports per batch. This information is also accessible through the operator interfaces and can interact with dashboards and trends to give you full access to include any of the reports in your data analysis workflow.
Reports are fully customizable, and can show/hide information depending on who is accessing them. Reports are also a great tool leading to our next and final Heat Treat Power Pack item…
Job Tracking
Job tracking serves two functions in heat treatment. It will help you manage your workflow and products as they move through the process, and allow you to share any jobs in progress with your customers (with a login so they will only see data relevant to them). This can ensure transparency across your process, keep your customers up to date without having to bother your team, and can allow you to easily share production reports and notes with no additional effort.
Job tracking is basically built into the Heat Treat Power Pack along with Work Order Management. Jobs are created along with the work orders. Their statuses are automatically updated as product moves through the process and operators start and complete batches. Data is automatically collected during production for each batch, and the reports are similarly automatically generated along the way.
Then, you have the option to show customers only information relevant to them in their job tracking interface, while giving your team anything and everything they need to manage production on the internal job tracking system.
Not only will this help you manage production more efficiently, it will also give you a leg up on the competition by using job tracking functionality as a selling point to your customers.
What is the Heat Treat Power Pack?
The Heat Treat Power Pack consists of the Ignition SCADA platform, layered on top of process automation hardware. If you already have automated furnaces using PLCs we can easily integrate with them. Or if you want to take your operation to the next level, we have trusted partners that fabricate furnaces and furnace controls and who can upgrade your existing equipment with modern controls. We’re also a certified partner of Made in the USA controls manufacturer, Opto 22 if you need additional modern control hardware or to interface with older systems—all in stock! We will do all of the programming and commissioning of those systems for you too.
What you get with the Heat Treat Power Pack:
Ignition SCADA System including Corso Systems Heat Treat Power Pack standardized functionality with:
Operator Interface/HMI screens
Process Historian for continuous data logging
Reporting capabilities
Job Tracking
Process Dashboards, Trends, and Data Analysis tools
Unlimited screens, data points, and users
A database to store all your logged data and job tracking information
PLC Programming to support automated operation of your equipment using our standardized heat treat control libraries
Ongoing support to help you get the most out of your system
Training for your team for managing and utilizing all of your new tools
Get Started Today!
Let’s take your heat treat process to the next level. Schedule a call with Cody Johnson in sales to learn what our Heat Treat Power Pack can do for you!
No sales pitch, just a candid conversation.