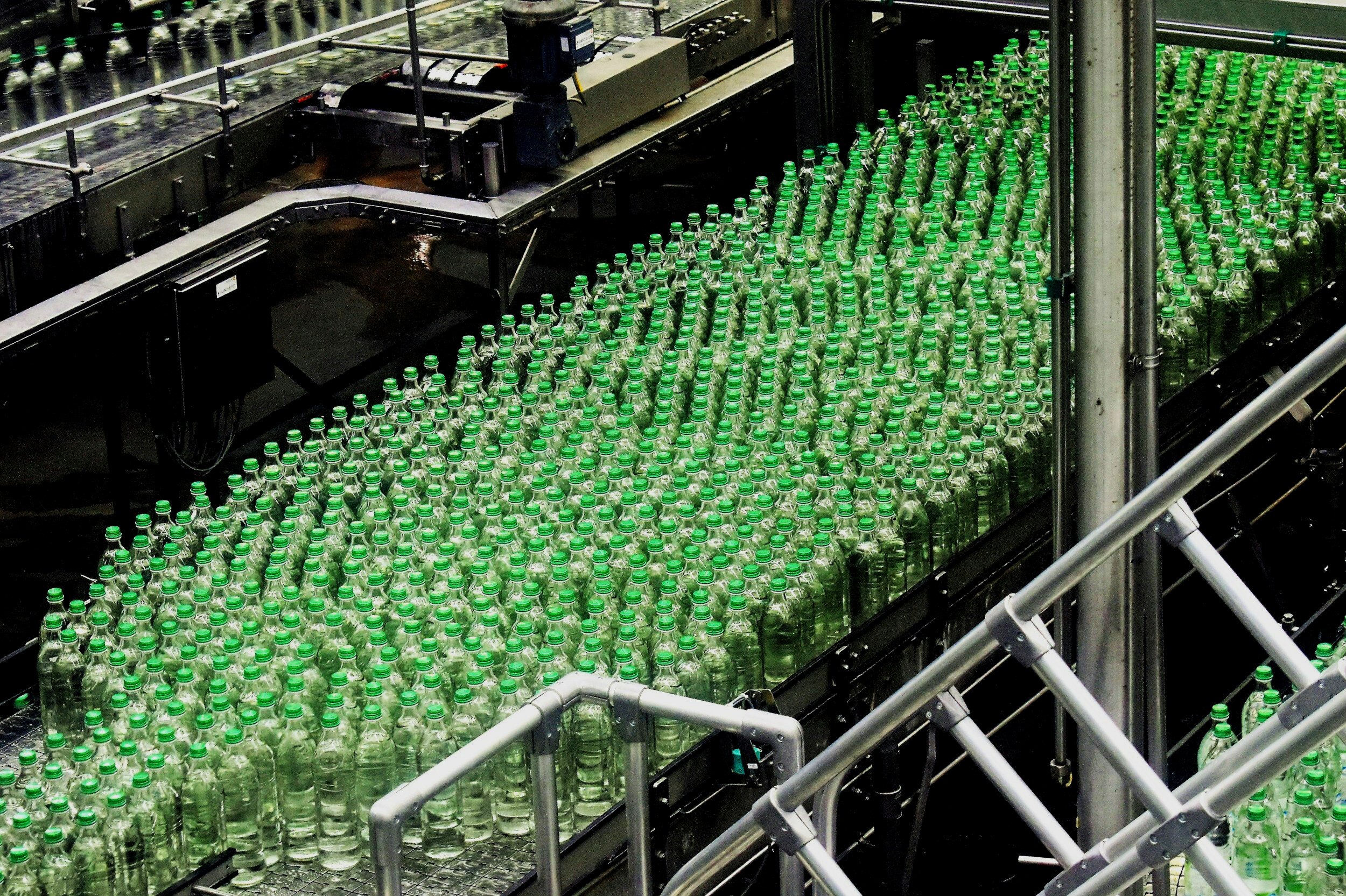
Food and Beverage Power Pack
Corso Systems has helped many food and beverage manufacturers standardize, streamline, and improve their operations. From breakfast, BBQ,brews, fast food, desserts, and candy, Corso Systems has helped companies across the entire meal spectrum power up their processes! While each company has unique processes and challenges, many of the strategies we and implement for our customers apply to all industries.
We believe transparency, technology (including automation), and training are the best tools for taking your manufacturing operations to the next level.
With all the advanced automation and auditable software tools available to Food and Beverage Manufacturers today, it is easier than ever to meet and maintain regulatory requirements. Technology can of course help on the plant floor, but now it can extend across the business. We can now integrate manufacturing processes with Quality Control systems, Shipping and Receiving, Warehouse and Inventory Management, Customer Service, and even energy and utility monitoring.
Introducing the Corso Systems Food & Beverage Power Pack
Food and Beverage Manufacturers will likely get the best ROI from improving their operations with automation and technology in five key areas. Each focuses on maintaining and improving quality, customer satisfaction, and enhancing overall peace of mind for your company.
Because many Food and Beverage Manufacturers can benefit from specific improvements in the following areas, we call them our Food and Beverage Power Pack:
If you’ve already implemented improvements and automation in one of more of these areas, great! If you are doing all of them, that’s even better! But, if you need help implementing (or improving) them for your Food and Beverage Manufacturing operations, you have come to the right place. Corso Systems can get you up and running quickly in any or all of these areas—with the tools to run your processes at their full potential!
In this post, we’ll explain each Food and Beverage Power Pack focus area below. The Corso Systems power pack is built with industry leading hardware and software that any company familiar with automation can work on or support. You will also have full access to all of the code included with the deployment—and of course you’ll own all of your data and information. We take care of the hard work for you.
Ready to Power Up Your Food & Bev Manufacturing Processes?
Book a 15-minute call with Cody Johnson in sales
No sales pitch, just a candid conversation.
Batch Tracking, Work Orders, and Scheduling
Unlike some manufacturing operations, Food and Beverage products are usually made in batches. While batches can be mapped to a single order, there’s often an overall batch spread across several work orders that will meet multiple customer orders.
To better understand your operation, you’ll need to know what needs to be made—and when. You’ll also need to manage how it gets made, and where inefficiencies are causing scheduling delays.
The Corso Systems Food and Beverage Power Pack builds the tools to manage batches, work orders, and production scheduling into the familiar systems your operators are already using.
Production Scheduling can build a schedule for your process. Production Managers and Operators execute the planned production. In the event of slowdowns, the system will automatically update everyone that they need to adjust future production.
These tools will integrate with your existing business systems to create batches on the floor, generate work orders for your products to propagate through the rest of their lifecycle, and will keep your team up to date for any batch.
Recipes & Variance Tracking
Recipes are critical for any successful Food and Beverage Manufacturing operation. While a Batch Management system will tell you WHAT to make, the production schedule will tell you WHEN to make it—and WHERE if you have multiple facilities, along with WHO. In most cases, we can assume the WHY is to make a profit.
Recipes tell us HOW to make product.
In manufacturing, recipes include raw ingredient amounts, process operations, and equipment setpoints. This information can be automatically managed in fully automated processes, or manually adjusted and monitored by operators. When necessary, you can also mix the two methods to combine manual ingredient additions with automated processes. (A common example is adding bulk goods like chocolate powder: operators need to manually add bags to a mixer while a delivery system automatically dispenses an exact amount of sugar.)
Recipes also tell the equipment how to run, including all times, temperatures, pressures, speeds, and feeds. Typically, a recipe is automatically sent to the process equipment to get everything ready for production before starting a batch.
While it is vitally important to tell the process how to operate, it is even more important to verify that equipment is running as expected with Recipe Variance Tracking. Recipe Variance Tracking monitors any and all data contained in your recipe and will log alerts if anything is different from an expected value. These alerts can be configured as alarms, or can simply be logged in the historian.
Recipe Variance Tracking also records when and what changes were made to the process—along with who made the changes. This information can be useful for training operators. It can also help your QA/QC team track down any quality issues. Additionally, data from Recipe Variance Tracking is useful for anyone on your team who needs to understand how to run the process more efficiently.
Production Dashboards, Trends, and Data Analysis
With a process running batches based on recipes (while collecting relevant data), production dashboards and trends can display what your equipment is doing.
Production Dashboards provide a real-time view into your process. You can observe trends in process data across your entire plant, energy/utility usage, and even quality control sample testing. These dashboards can be consolidated in a control room, or displayed across the plant floor to give your operators convenient access to the information they need.
You can use trending and reporting tools to drill into your data in real-time or historically. By comparing the current batch against previous batches, you can evaluate how you are performing and quickly spot any anomalies. You can even save a particularly good batch as a “Golden Batch” to use as the gold standard for measuring performance.
Your new automation system can export data from any batch to Excel or other data analysis tools, so that you and your team can dig into the data with your favorite or familiar methods.
Reports
If dashboards and trends are useful for operators while running the process, reports are useful as summaries of what happened during a given batch. Depending on your regulatory requirements, these reports can even be automated to simplify compliance.
With Corso Systems’ Food and Beverage Power Pack reporting functionality, you can easily generate reports for any time range—daily, weekly, monthly, or any custom length of time. We can also generate reports for batches triggered by start and end times, or even specialized reports for tracking anomalies with detailed information for your records.
These reports can be stored electronically as PDFs, or emailed, printed, and summarized into a single file at the end of a batch (if you are generating multiple reports per batch). Reports can also be accessible through operator interfaces and can interact with dashboards and trends to include full access to any of the reports in your data analysis workflow.
Reports are fully customizable, and can show/hide information depending on the user who accessing them.
Quality Control
Automation and SCADA systems have emerged as game-changers for quality control departments. The Food and Beverage Power Pack simplifies quality management, while optimizing and significantly improving the efficiency of quality control processes within your facility.
One of the primary advantages of integrating a quality control management system for food and beverage manufacturing is the real-time visibility it provides. Real-time data access allows for quick identification of any deviations or anomalies in the manufacturing process, facilitating proactive decision-making and timely interventions to maintain product quality. You can even schedule and manage manual sample collection in your process.
Integrating SCADA with a quality control management system enhances the overall efficiency of quality control by automating routine tasks. Since SCADA integrated process control systems enable automated data collection and analysis, this reduces the manual workload for quality control personnel. Quality control teams can then minimize human error risks and focus on the more complex and strategic aspects of their responsibilities.
Optimizing quality control processes through SCADA and process control integration extends beyond mere efficiency gains. It gives manufacturing facilities the power to implement sophisticated quality control algorithms. By leveraging real-time data, these algorithms can identify patterns, predict potential quality issues, and automatically adjust production parameters to ensure consistent product quality. This predictive and adaptive approach streamlines the quality control process and minimizes the likelihood of defects or variations in the final product.
The Corso Systems Food and Beverage Power Pack unlocks all of these powerful capabilities. From automating sample collection, simplifying data management and analysis, all the way up to a full-blown Statistical Process Control (SPC) system, we can help you do it all!
Intrigued?
Book a 15-minute call with Cody, the Corso Systems Head of Sales
No sales pitch, just a candid conversation.
What is the Food and Beverage Power Pack?
The Food and Beverage Power Pack consists of the Ignition SCADA platform, layered with process automation hardware and system integrations with business systems like your ERP. Assuming you already have PLC controlled automated equipment, we can easily integrate with it, and can handle any manual processes you may have.
If you require additional automation hardware, we can help spec out exactly what you need with our trusted partners (including US-based controls manufacturer, Opto 22), program and integrate it, and help take your operation to the next level!
What you get with the Food and Beverage Power Pack:
Ignition SCADA System including Corso Systems Food and Beverage Power Pack standardized functionality with:
Operator Interface/HMI screens
Process Historian for continuous data logging
Batch, Work Order, and Schedule Management
Recipe Tracking and Management
Process Dashboards, Trends, and Data Analysis tools
Reporting capabilities
Quality Control Management Systems and SPC Integrations
Unlimited screens, data points, and users
A database to store all logged data and operations information
PLC programming to support automated operation of your equipment using our standardized process control libraries
Ongoing support to help you get the most from your system
Training for your team to manage and use all your new systems and tools
Get Started Today!
Corso Systems can take your Food and Beverage Manufacturing process to the next level. Schedule a call with Cody Johnson in sales to learn what our Food and Beverage Power Pack can do for you!
No sales pitch, just a candid conversation.