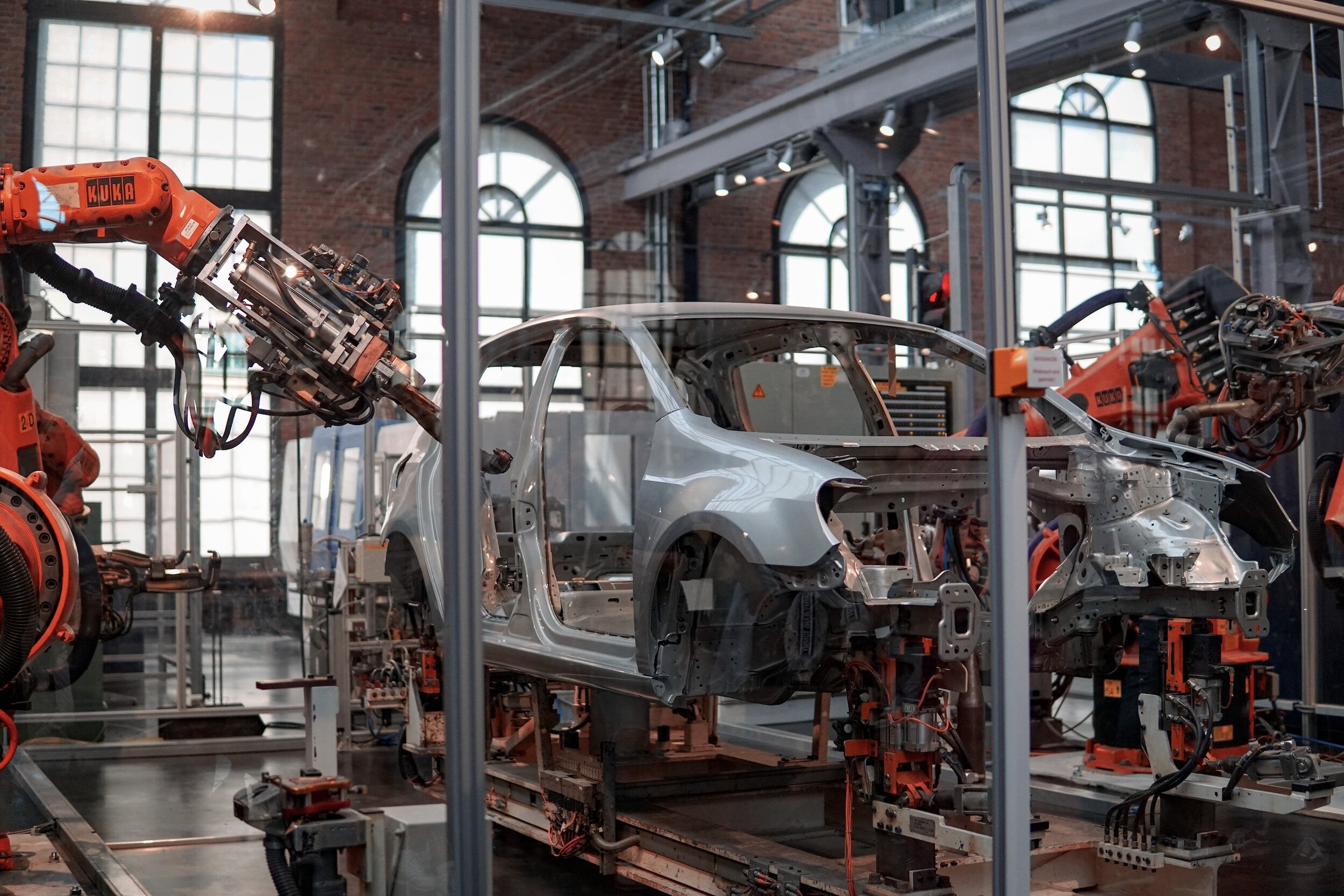
Automotive Power Pack
Corso Systems has helped many automotive manufacturing companies standardize, optimize, and automate their manufacturing operations. We’ve worked with it all—from fully automated production lines at the largest manufacturing facility in the world, to building data analysis tools for one of the most technologically advanced manufacturing processes in a retrofitted building from 1980s. We’ve also improved many commonplace heat treatment, paint, and assembly processes too.
Regardless of what you manufacture, we believe transparency, technology (including automation), and training are the best tools to take your manufacturing operations to the next level.
With the advent of new tools and sensors Automotive Manufacturing is a great industry for applying Track and Traceability frameworks to manage product recalls and document vehicles as they move through the line. With high production volumes common in most facilities advanced data analysis and dashboard tools can help teams manage complex manufacturing lines with ease, and with large scale facilities mobile devices and modern interfaces like Maps can be used to get a detailed glimpse into any portion of the process wherever you are.
Introducing the Corso Systems Automotive Power Pack
In our experience, automotive manufacturers can improve their process and profitability by focusing on five specific areas. Working on these areas will also maintain and improve quality, improve customer satisfaction, and enhance overall peace of mind at your company.
Our Automotive Power Pack focuses on these five areas:
If you’ve already implemented automation within some or all of these areas, great! But, if you need help improving your process and production operation, you have come to the right place. We can have your facility up and running quickly in any or all of these areas with the tools to run your processes at their full potential!
In this post, we’ll explain each aspect of the Corso Systems Automotive Power Pack. It’s built with well known industry leading automation hardware and software. You will also have full access to all of the code included with the deployment—and you will always own all of your data and information. We will take care of the hard work for you.
Ready to Power Up Your Processes?
Book a 15-minute call with Cody Johnson in sales
No sales pitch, just a candid conversation.
Facilities and Process Utility Management
Even the most advanced, fully robotic, automated production line is only as good as the utilities and facilities supporting all the equipment. If you don’t have power, water, compressed air, hydraulics, steam, or any other common utilities required by your process, you won’t be able to produce product!
One of the first and most critical tasks we tackle at new automotive facilities is to make sure they have a solid handle on their Facility and Utility Management screens. This involves monitoring all the systems, enabling control where needed, and sending out alarm notifications to staff and operators need to know about them to keep everything running smoothly.
A Facilities Management System will integrate with devices in the switchgear for the building, the electrical circuits, and control panels with alarms and alerts for power quality or power sourcing issues. The system can expand into monitoring/controlling compressed air, cooling water and water treatment systems, air and liquid compressor systems, and even boilers and steam systems where applicable.
Taking advantage of the Mobile and Map-Based SCADA solution detailed below in this post, our Automotive Power Pack allows your team to manage your supporting infrastructure from any location.
With the Ignition SCADA platform, you also get the ability to directly connect with the most common industry protocols for utilities and facility management: DNP3, BACnet, Modbus, and Ethernet/IP. Plus, you can interface these systems with any other process controls and robotics through Ignition directly.
Track and Trace
With the Digital Transformation of the past decade, it’s easier than ever to automate data collection down to literally each individual nut and bolt tightened to a particular tolerance on a chassis. Track and Trace information can include the details about which nuts and bolts are used, when the torque wrench was calibrated, and when the operator was last trained on its operation. You could even add in ambient temperature and humidity readings, noise levels, along with detailed information such as part manufacturer’s lot numbers for every part involved.
All of this information is integrated with your ERP system to a vehicle’s VIN number. In the event of a product recall, this information can be quickly retrieved to find and alert affected customers. Track and Trace allows manufacturers to pinpoint and contact the exact customers affected.
Compared to the old days of clipboards and inspections there is no reason not to take advantage of this technology. It is the right thing to do by your customers and helps you maintain regulatory compliance. It also helps you build trust and support your customers by being able to proactively reach out to them in the event something needs addressed on their vehicle.
Our Automotive Power Pack gets you started with everything you need to begin collecting any and all track and trace data about your production lines along with the reporting tools required to find affected vehicles across your entire production lifecycle.
It’s Time to Track, Trace, Transform!
Book a 15-minute call with Corso Systems sales
No sales pitch, just a candid conversation.
Mobile and Map-Based SCADA
Automotive Manufacturing plants are some of the largest manufacturing facilities in the world. While operators will typically have a hyper-local focus on a single area of the line (or an individual work station), the maintenance staff, higher level production staff, and supervisors need to monitor many places at once.
The Ignition Perspective Module helps solve the problem of needing to be in multiple places at once. Using mobile SCADA screens can speed up decision making—your team can access critical data and alarms right when they need it. Instead of needing to find a computer on the floor, walk back to a control room, or their office, they can access a dashboard on their phone, see the current state of any equipment in the facility and decide what needs to be done on the spot. This same technology can also apply to overall compliance and quality control because your team can enter readings and notes for anything they need to measure right on the spot. No need for pencil and paper to later transfer “to the system” manually back at their desks.
Mobile SCADA also enhances the collaboration opportunities available to your team. Different teams can share real-time data and examine it together on their phones or tablets. Combined with plant floor dashboards and HMI displays, they can get a full picture of the current state of operations along with the context provided by historical data and data analysis tools.
Location tracking on mobile devices can improve safety by tracking the real-time location of your staff members in an emergency.
For large scale facilities, using a Map-Based SCADA screen provides a complete view of your plant with different levels of detail as you zoom into the floor. Dashboards, KPIs and status indicators for every production area, individual line, work cell, and piece of equipment can be added to the screen, giving you access to any level of detail you need. For additional detail, zoom in on a particular area and your view will update accordingly.
Unified Namespace for Overall Data Management
As we’ve covered in our Unified Namespace: The Ultimate Guide, a Unified Namespace (UNS) simplifies the flow of information across an entire enterprise, giving you insight on everything from the shop floor to the top floor.
A Unified Namespace can map out your overall business including customer service, shipping and receiving, warehousing, facilities and utilities, and your entire production operation. You can drill down further in these functional areas, and follow the ISA-95 hierarchy for production lines with the flexibility to model the rest of the business as needed.
Each area sends data to the Unified Namespace from each integrated system so that you can see the entire state of your business as it stands in real time. This approach allows you to standardize your data map for process lines, equipment, and operations, reducing training time to get people up to speed across the plant, and simplifying specifications for new equipment or data points you need to add later.
Building out a Unified Namespace along with advanced reporting and dashboard tools gives you the ability to easily build dynamic systems to examine other areas of the plant without excessive configuration.
The Unified Namespace can also simplify building out a Map-Based SCADA system. By including coordinates in the plant for specific pieces of equipment in the UNS, you can automatically generate all of the KPI and Dashboard instances on the map itself, simplifying deployment of the overall Map interface.
Corso Systems has helped many companies across various industries implement UNS for their organizations and we include this service and the work of mapping everything out as part of our Automotive Power Pack.
Power Up With the Automotive Power Pack!
Book a 15-minute call with Corso Systems sales
No sales pitch, just a candid conversation.
Dynamic Reporting and Dashboards
Dynamic reports and dashboards play a crucial role in optimizing operations and decision-making processes within an automotive manufacturing facility. These tools leverage real-time data visualization and analytics to provide a comprehensive, up-to-date overview of the manufacturing process.
The first and most common use for dynamic dashboards is real-time monitoring and performance tracking of the process, including metrics like OEE. This gives your team a real-time view into the health of production, any issues preventing vehicles from moving out the door, and if slowdowns affecting how many vehicles are moving through the line.
Using this information allows you to allocate resources to your process more efficiently, reduce bottlenecks, and ensure you are meeting your production schedules. Combined with a warehouse management system, tracking production in real-time also helps you manage inventory and gives you visibility to your overall supply chain. This can reduce downtime for parts to be delivered to the line, and can alert warehouse staff to bring materials before there’s a production slowdown.
Many manufacturers also use dashboards to track quality control issues and defects. This simplifies re-work and can help estimate when a vehicle will be close to completion.
Your team can easily customize dashboards for their specific needs. Supervisors can build tracking tools for shift standup meetings, managers can track overall production on any given line. You can track the overall health of the business at the C-Suite level by tying into the overall Unified Namespace for the business to correlate data across the company.
Dynamic reports and dashboards provide an invaluable toolset for automotive manufacturing facilities with real-time insights, enhanced decision-making processes, optimized resource utilization, improved quality control, and overall operational excellence. This is why dynamic reports and dashboards are a key component of the Automotive Power Pack.
What is the Automotive Power Pack?
The Automotive Power Pack consists of the Ignition SCADA platform and process automation hardware. If you already have automated equipment with PLCs we can easily integrate with them. Or if you want to take your operation to the next level, we have trusted partners (including US-based controls manufacturer, Opto 22) who can work with us to upgrade your existing equipment with modern controls. We can also program and commission those systems for you too!
What you get with the Automotive Power Pack:
Ignition SCADA System including Corso Systems Automotive Power Pack standardized functionality with:
Operator Interface/HMI screens
Process Historian for continuous data logging
Facilities and Process Utility Management
Track and Traceability Systems
Mobile and Map-Based SCADA Solutions
Unified Namespace for Overall Data Management
Dynamic Reporting and Dashboards
Unlimited screens, data points, and users
A database to store all your logged data and job tracking information
PLC Programming to support automated operation of your equipment using our standardized control libraries
Ongoing support to help you get the most out of your system
Training for your team for managing and utilizing all of your new tools
Get Started Today!
Let’s take your automotive manufacturing process to the next level. Schedule a call with Cody Johnson in sales to learn what our Automotive Power Pack can do for you!
No sales pitch, just a candid conversation.